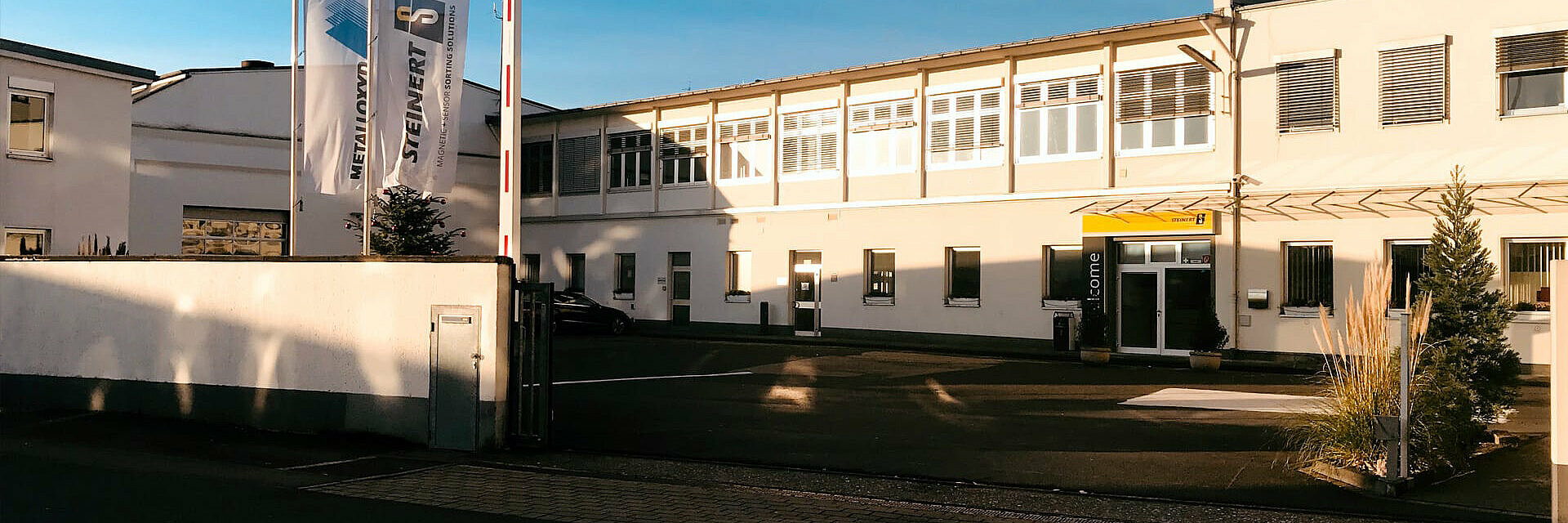
HISTORY
Firmly-rooted in the future
STEINERT, founded by Ferdinand Steinert, can look back over a long and diverse history. Documents more than 100 years old provide evidence of our founder’s pioneering achievements; steeped in history, they are the starting point for an ongoing journey starting with the separation of compact clumps of iron right up to the high-tech filtering of delicate micro-particles. Right from the start, the objective of the founder Ferdinand Steinert was clear: efficient recycling!
Delve into the interesting facts and figures documenting our exciting history.
STEINERT acquires MSort product range
2024
The purchase led to the founding of the subsidiary STEINERT MSort GmbH, which can now offer new sorting solutions and expands the portfolio to include transmitted light and double-sided detection using colour and near-infrared (NIR). The company is based in Wedel near Hamburg. The focus is on the processing of flat and hollow glass and the sorting of industrial minerals for the mining industry.
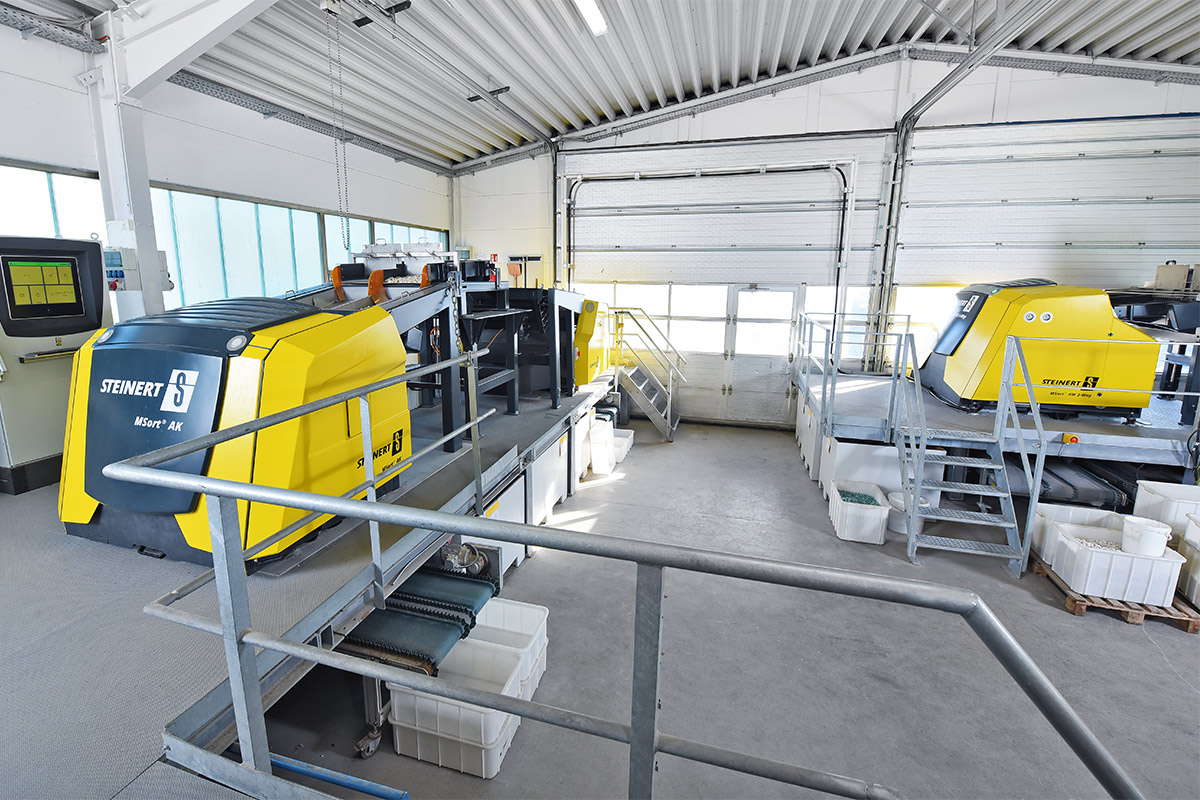
New office and production building in Brazil
2023
After the company premises of STEINERT Latin America fell victim to a devastating fire, the new office and production building was officially opened in late summer 2023.

Opening of the new multifunctional building on the site of the Cologne headquarters
2022
As the first part of a master plan to optimize the long-term use of the Cologne site, the new multifunctional building was put into operation in 2022. This enabled production capacities to be increased and warehouse logistics to be optimized.

Opening of the Test and Development Center
2020
On September 22nd, 2020, STEINERT again demonstrates the way forward. STEINERT opens its Test and Development Center in Pulheim, just 4 miles as the crow flies from the company’s headquarters in Cologne.
The impressive figures speak for themselves; While STEINERT welcomed over 500 visitors a year to its old test centre, at around 38,000 sq ft, the new site has almost three times the space. The new test facility has 984 feet of conveyor belt and more than 35 highly-skilled staff that work on the 3 separate sorting lines for metal recycling, waste recycling and mining, delivering technical innovations and highly efficient test procedures.
As part of their visits and material tests, customers can now benefit from the most recent developments to an even greater extent and see the entire range of applications for themselves: from magnetic separators to sensor-based sorting systems, such as X-ray transmission, X-ray fluorescence and near-infrared.

Combining sensors and responding flexibly to the future
2018
Our STEINERT KSS (combination sorting system) is a platform for various sensors which includes 3D, colour and induction recognition. The system can also be fitted with a fourth sensor (near-infrared, X-ray transmission or X-ray fluorescence sensor). The software developed in-house at STEINERT also allows new recognition algorithms to be produced and, if necessary, used at short notice to overcome new challenges.
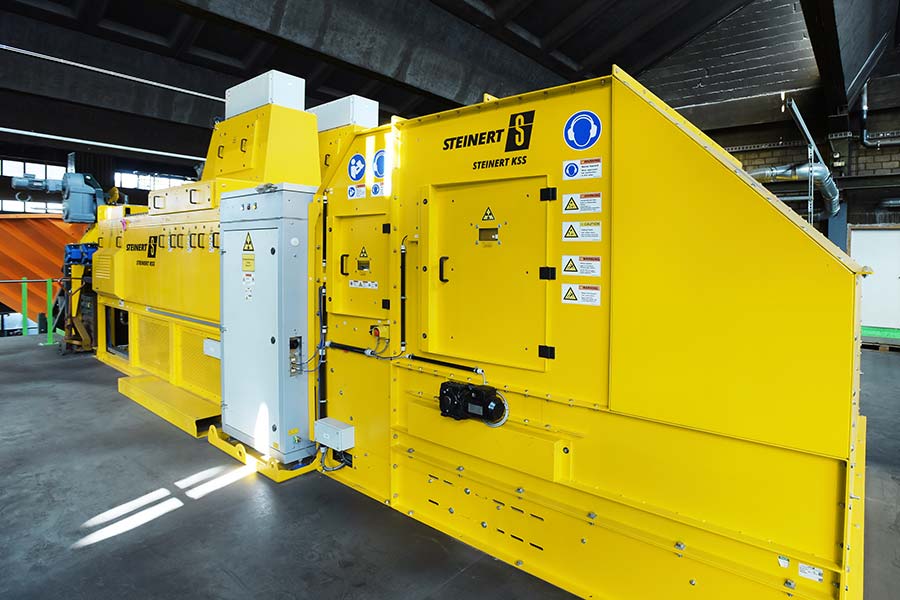
Separation of black plastics added to the range
2016
By launching the UniSort BlackEye, STEINERT once again demonstrates its pioneering spirit in the development of leading technologies. The sensor-based sorting system does not only separate plastics by colour, but also by polymer class (PE, PP, PVC and styrene). The UniSort BlackEye can therefore correctly separate black plastics by plastic type. One feature of particular interest in terms of rates of recycling is the ability to distinguish between PE and PP. Since most packaging comprises PE and PP, they can be accurately captured in sorting facilities. A large proportion of black polyolefins is also used in the automotive sector.
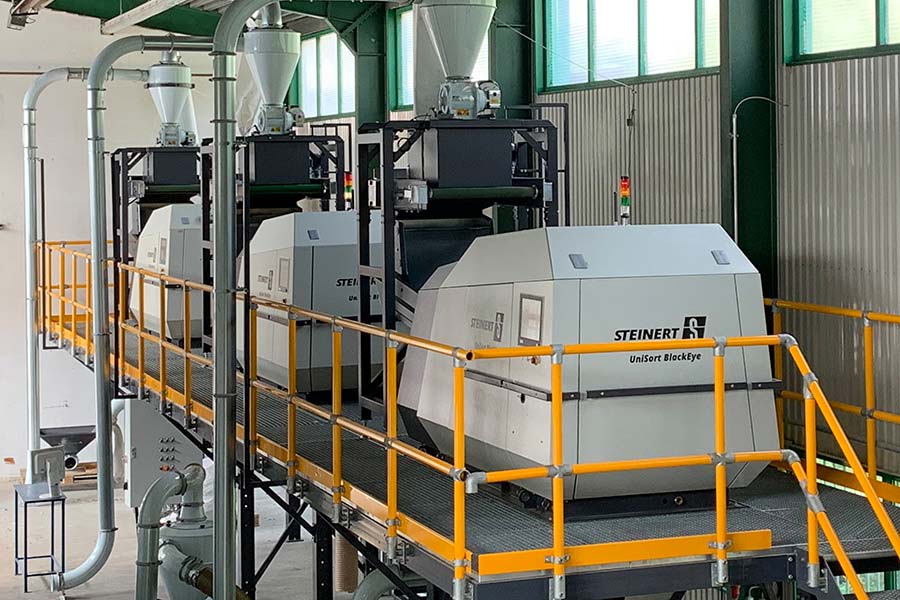
NIR technology introduced and the USA increases capacities
2009
The majority takeover of RTT Systemtechnik GmbH in Zittau and the name change to RTT STEINERT GmbH in 2009 extends the product range yet further: near-infrared technology (NIR) is added to the portfolio. Typical patterns for materials based on molecular vibrations can be detected in the NIR wavelength range (1000 and 1700 nm) after excitation with light. The UniSort brand is developed and enters production. UniSort remains synonymous with superior sorting systems, predominantly in the field of waste recycling. In the same year, the STEINERT US headquarters move into a larger facility in Cincinnati.
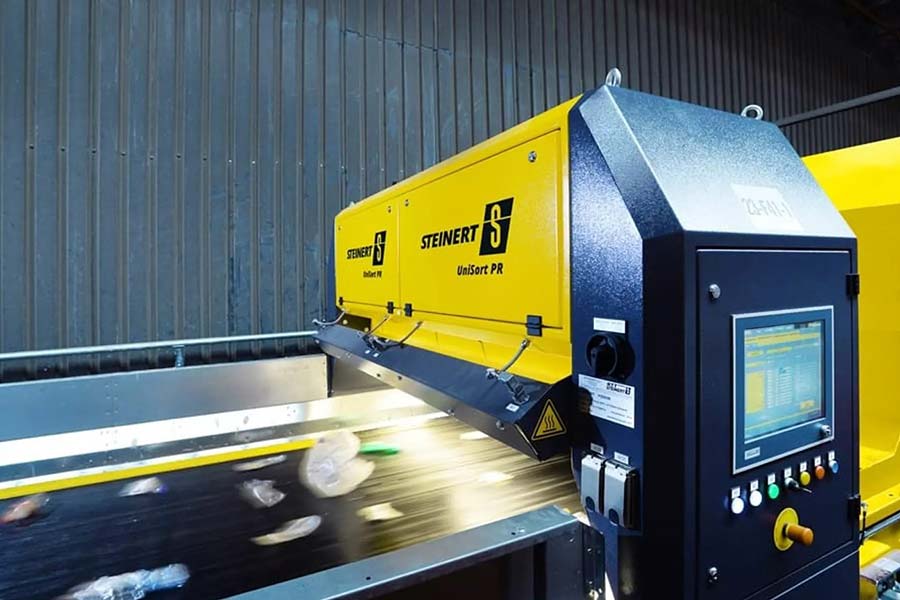
STEINERT in Brazil
2007
By founding STEINERT Latinoamericana, STEINERT establishes a third subsidiary within the network of affiliated companies and demonstrates its commitment to Central and South America. Locating the new company close to customers and market activities enables excellent service and support in Central and South America too. Based in the Castelo district of Belo Horizonte in Minas Gerais, STEINERT is strategically positioned in a zone of importance to the mining industry. Going forward, the mining and recycling industries will be able to benefit from services, commissioning work, maintenance and training courses from colleagues in their own country.
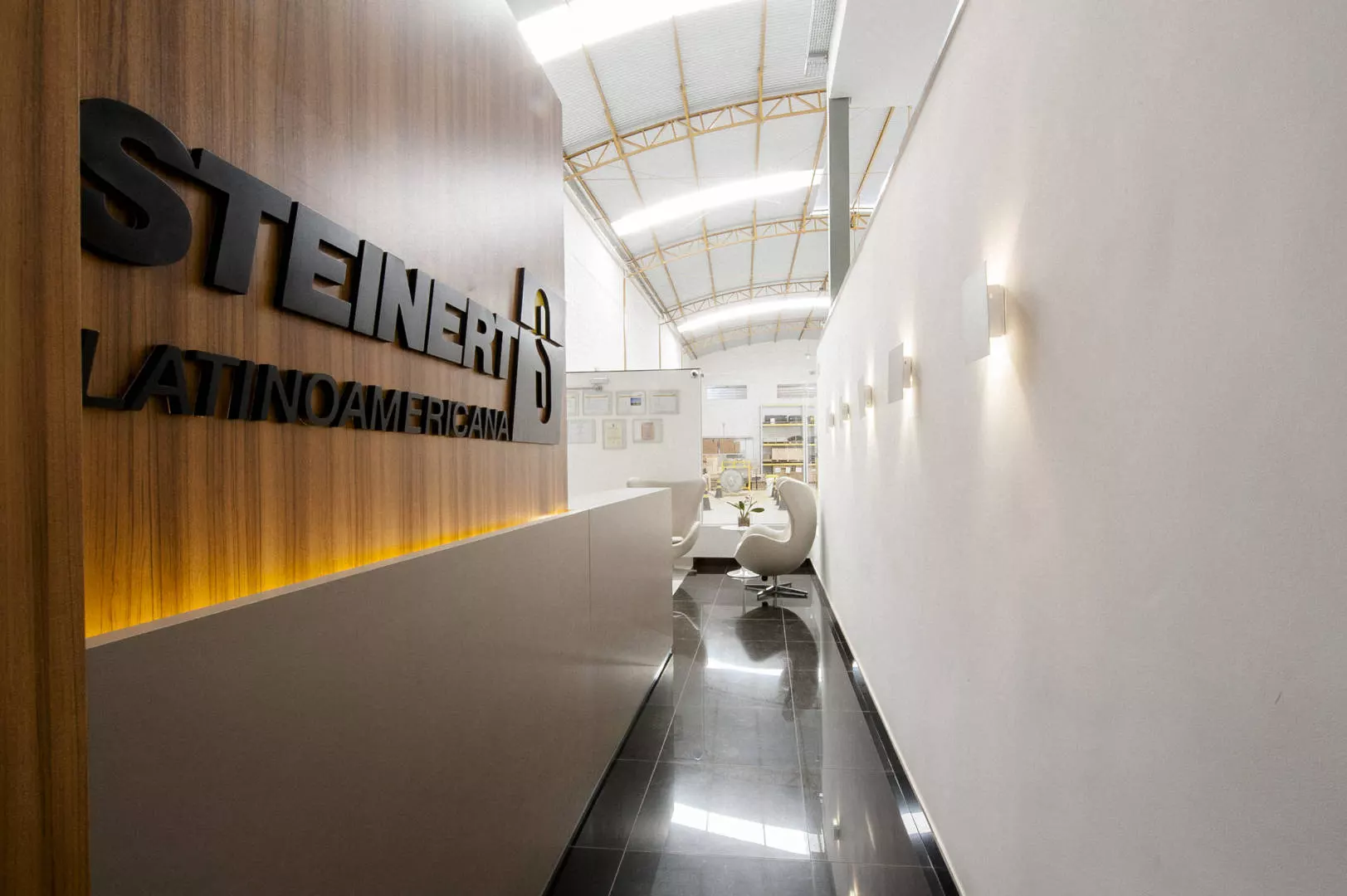
Strong presence in Oceania
2004
STEINERT has owned Australia-based Sturton-Gill since 2004. It has traded under the name of STEINERT Australia Pty. Ltd. since 2009 and has its headquarters in Melbourne. STEINERT Australia is one of the leading manufacturers of magnets in the Asia-Pacific region and is a supplier to the expanding local recycling industry and the powerful mining industry. It now has its own Test Center for sensor-based sorting in Perth on the west coast of Australia, enabling customers to conduct their own tests with their own material. This enables them to test out their requirements, feasibility and ROI of any planned investments before committing to the purchase.
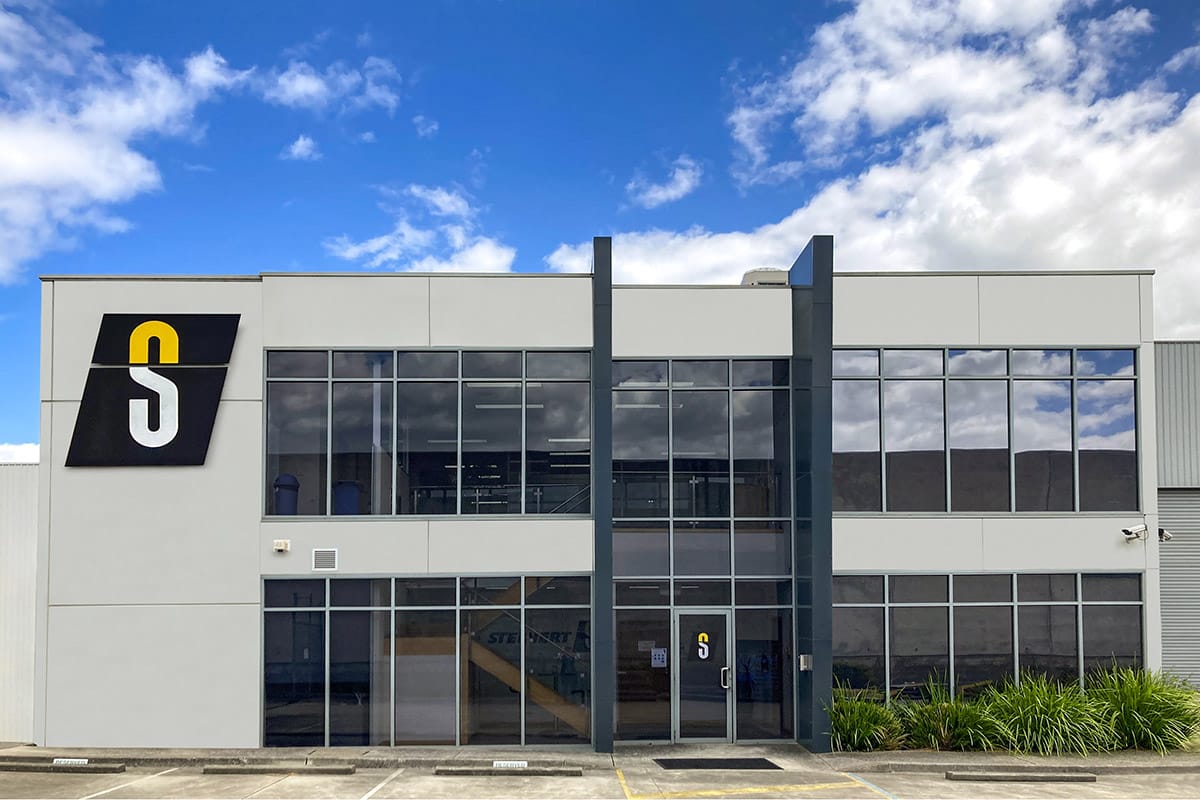
Founding of STEINERT US
2003
Huge demand on the North American market resulted in the founding of STEINERT US Ltd. in St. Petersburg, Florida. North American customers are quickly able to benefit from the well-developed infrastructure. The local team now delivers service and maintenance work on site much faster and more directly. STEINERT US also produces individual magnetic separators itself on site. The market responds to these moves by placing even more orders. Close proximity to customers and the great service team have proven to be huge factors for success in the USA.
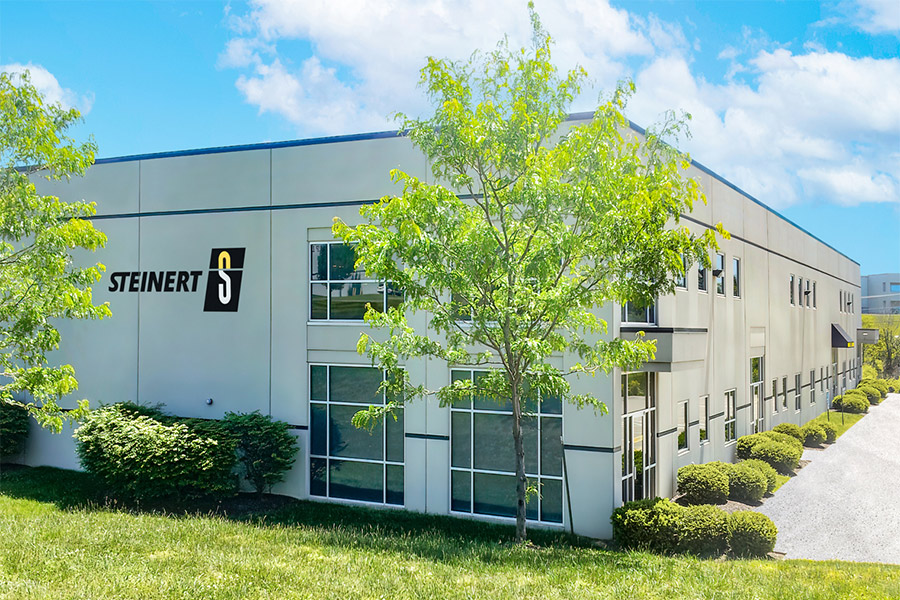
Recovery from liquids too
2002
The company enters a new sector by developing and presenting the STEINERT HGF high-gradient magnetic filter. The matrix separator with permanent magnets enables incredibly fine magnetic elements to be removed from process liquids, such as degreasing baths in the steel industry, for the first time with an efficiency of more than 90%. Many steel companies have at least one such STEINERT HGF in operation.
What’s more, the magnetic filter has also gained a firm foothold in biotechnology. In 2003, the STEINERT HGS high gradient magnetic separator is presented. This separates the finest magnetic components out of both salt and construction chemicals.
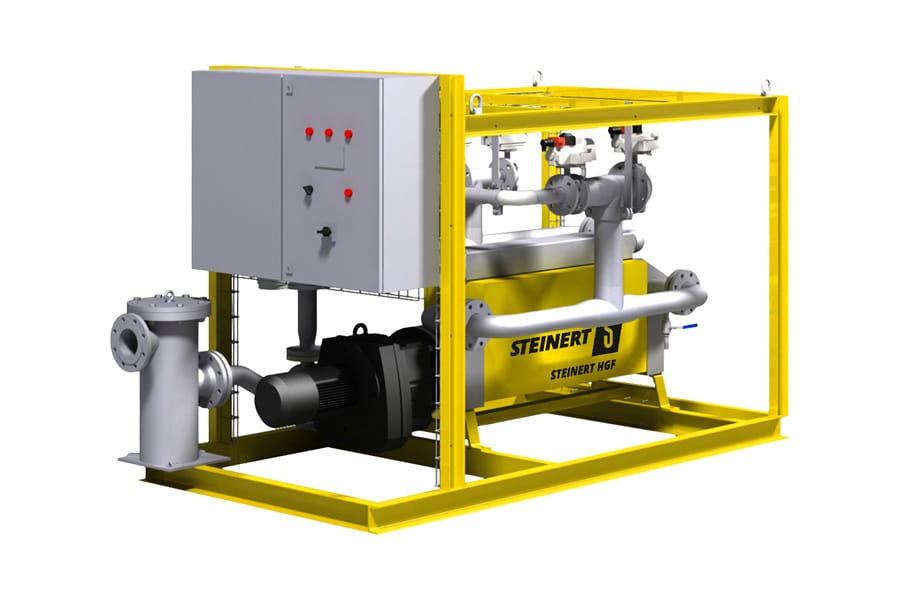
New technologies and expansion
2000
The new millennium starts with a new generation and expansion of research and development. The next few years will not only see new but also unique sorting systems appear on the market. New subsidiaries and sales partnerships also reinforce STEINERT’s global presence.
Advances made in sensors and data processing enable the development of colour sorting systems and the STEINERT ISS® induction sorting system. Both technologies aim to further increase yield and purity in metal recycling. In parallel to this, new markets open up in RDF treatment, wood treatment and plastic recycling.
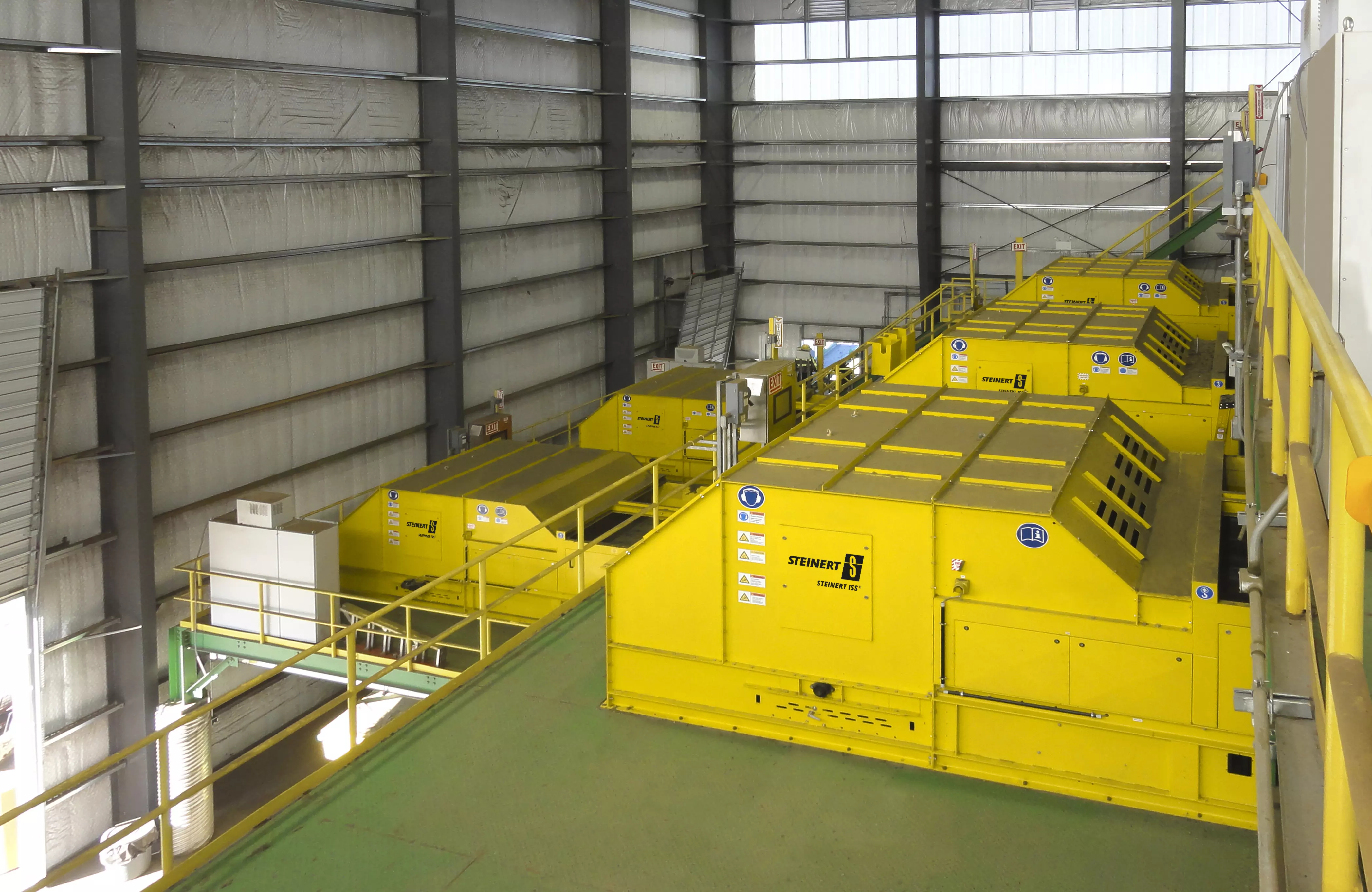
Further development of the non-ferrous metals separator
1996
The focus of work in the recycling industry increasingly moves in the direction of recovering particularly fine non-ferrous metals. STEINERT further develops the non-ferrous metal separator in response to this demand. Since the alternating pole frequency is of particular importance for the induction of eddy currents in small particle sizes, a so-called fine pole system is used for this type. This development should also prove to be a success. STEINERT is still a pioneer in this field.

The non-ferrous metals separator with an eccentric pole system
1987
STEINERT presents the first eccentric non-ferrous metals separator. This eddy current separator (also known as ECS or eddy) is used to recover non-ferrous metals, such as aluminium, copper or brass. The patented, eccentric pole system ensures that the magnetic field's influence is only at its highest at the moment of separation and a field is not generated at other points in the belt drum. Today, non-ferrous metals separators form the commercial basis of any recycling, and more than 5000 of STEINERT’s separators alone are deployed worldwide in sorting and processing facilities.
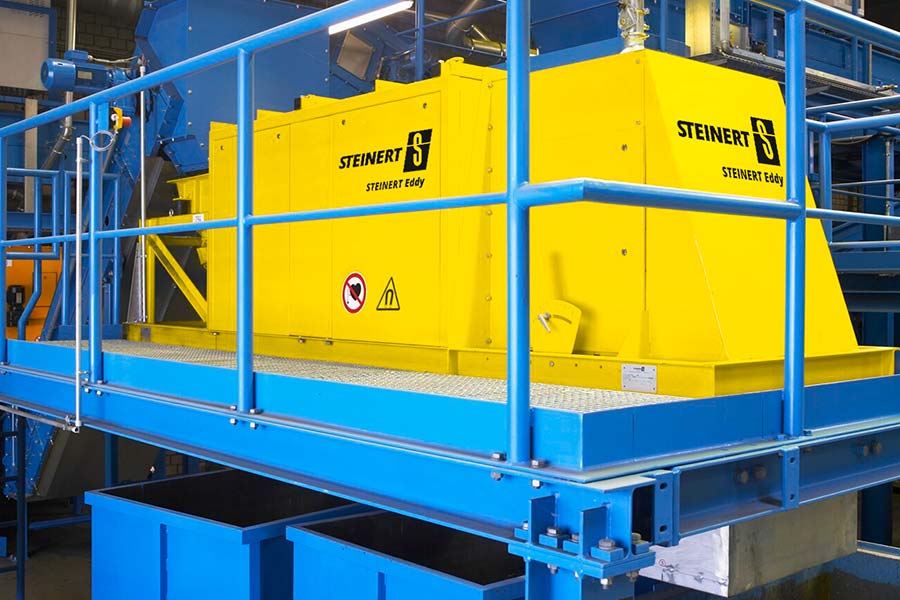
Use ofanodised aluminium strips in coils for magnets
1969
The Metalloxyd parent company has been developing an innovative product since way back towards the end of the 1950s: the anodised ANOFOL® strip. From 1969 onwards, it was used as the conductor material for lifting and self-cleaning overhead suspension magnets. While American competitors use conventional copper windings in coils, STEINERT is the first to use anodised aluminium strips. The compact coil, which can thereby be produced, is distinguished mainly by its excellent fill factor and extremely good heat dissipation. This innovation propels STEINERT further to the fore and is also successfully deployed in other industries. While the market share of lifting magnets declines due to changes in the economic environment, the requirements of separation technology continue to grow.
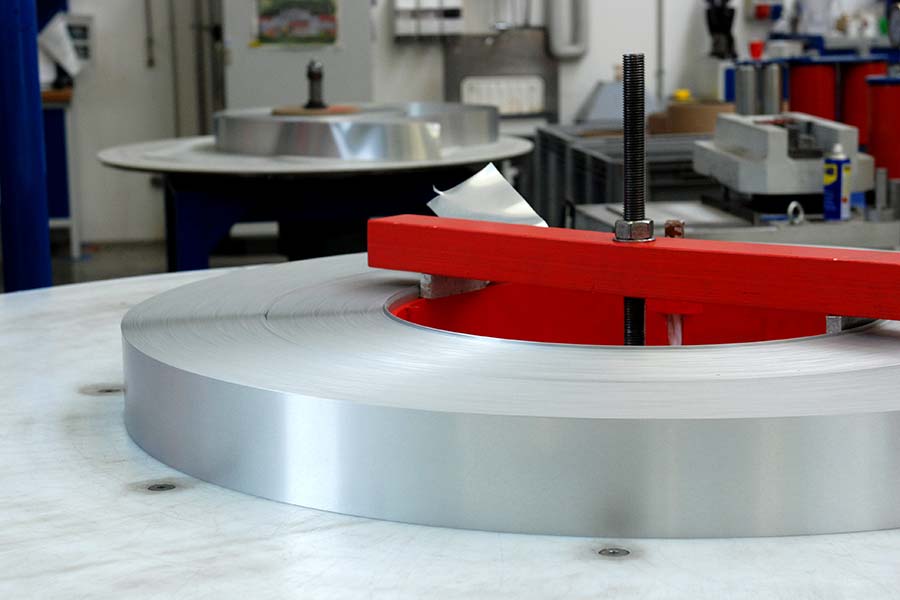
The new lifting magnets
1963
Following years of reconstruction, STEINERT quickly writes the next chapter of its success story. In 1963, the company presents the prototype of a new range of lifting magnets on its own stand at a trade fair in Hanover. Benefits include its low weight, greater magnetic power and low price. At the same time, waste treatment and recycling gain in importance. Dwindling resources, calls for environmental protection and an explosion in costs on the raw materials market make new technologies necessary. STEINERT rises to these challenges with immense passion and develops new products.
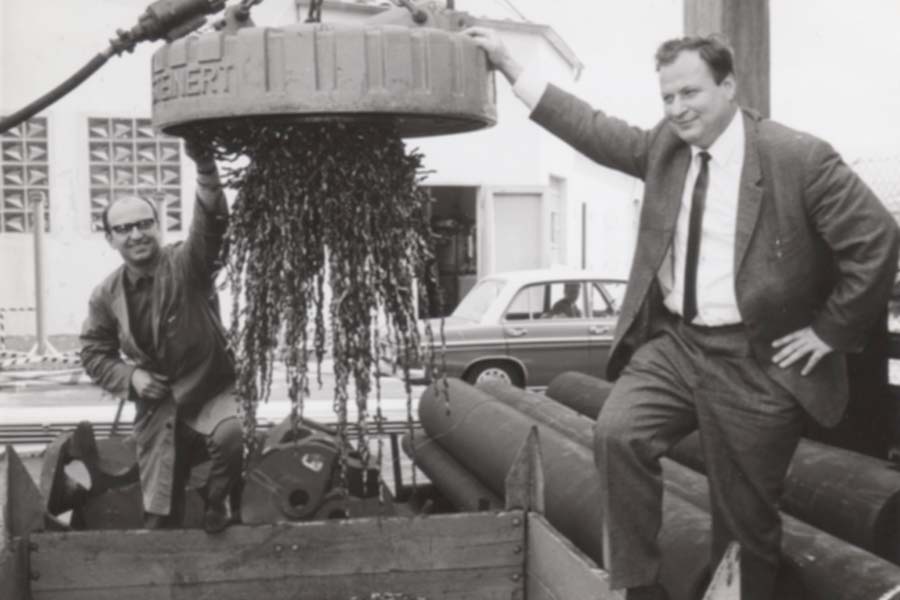
The first overhead suspension magnet
1960
In 1960, STEINERT presents the first overhead suspension magnet. This magnet recovers iron from shredder material, municipal solid waste, demolition waste, waste and steelwork slag. In mining, they are mainly used to protect crushers, mills and other mining processing equipment from wear and destruction by removing harmful ferrous parts, such as bolts, nuts and rock bolts from coal, coke, ore and other minerals and ores. The self-cleaning overhead suspension magnet is arranged above a feeding conveyor belt and extracts the ferromagnetic materials from the supply flow against the force of gravity. Several thousand of these machines are put into use around the globe over the next few years.
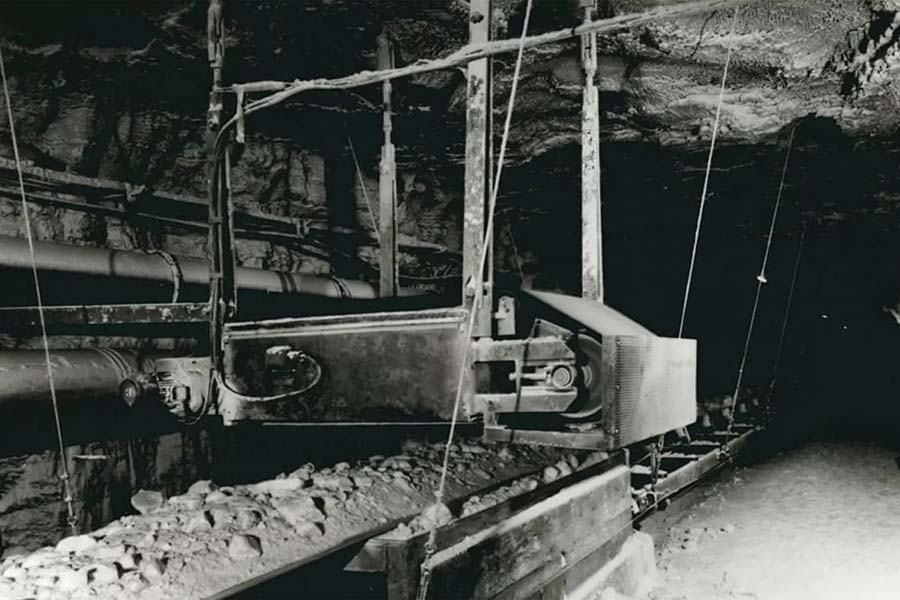
The birth of a strong corporate group
1931
In 1931, Julius Christian Buchholz buys the company. The birth of the Metalloxyd holding company contributes to the expansion of the market position. STEINERT and the Metalloxyd holding company are a perfect match for one another. One of the first major results of the merger is the breakthrough in anodic oxidation. During the Second World War, most of the premises in Cologne are destroyed. But management and the workforce reconstruct the company and extend the product range. STEINERT becomes established on the international market.
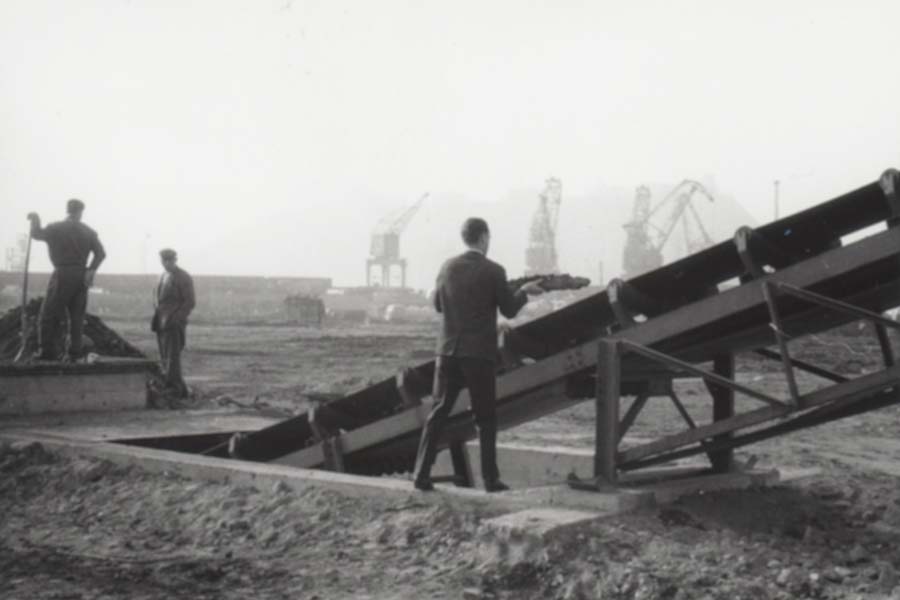
STEINERT grows with the trends of the time
1900
At the start of the new century, the economic conditions are ideal for the new company. The order books are full and customers are flooding in from mining, shipping and the steel industry. Separator magnets no longer have to work with chunky hammers or iron lugs alone, the objects to be separated are getting smaller, and the technology involved is becoming ever more complex. Increasingly, the magnets working in coal pits have to reliably separate smaller waste products, like thin wires or bent drill rods, out of bulk material. At the same time, the market for lifting magnets is growing.
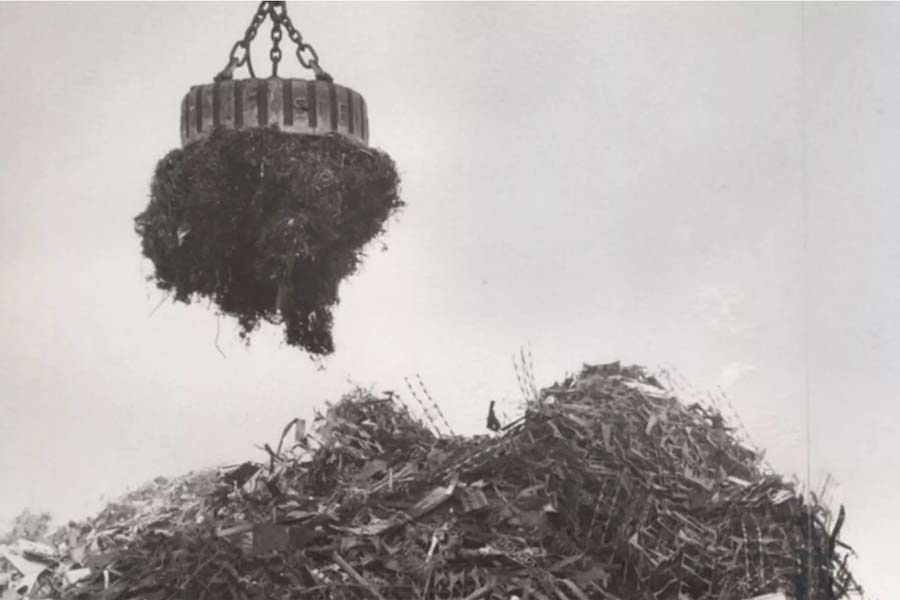
Founding of STEINERT
1889
In 1889, Ferdinand Steinert founds “Ferdinand STEINERT Elektromagnetische Aufbereitungsanlagen” in Cologne. The new company initially works in small structures, but the market for the use of separation magnets is huge. While we have been aware of the phenomenon of magnetism since the eleventh century, it has so far been put to very little economic use.
The steel industry is one of the company's first customers. The design engineer Ferdinand Steinert develops magnets, which are used to recover iron from steel slag and steel waste, and from waste in foundries and iron works. It’s an effective procedure, which soon becomes more widespread as it becomes possible to separate coal from slag too. This further technical refinement is of great interest to the state railways, for example, which become a major client of STEINERT.
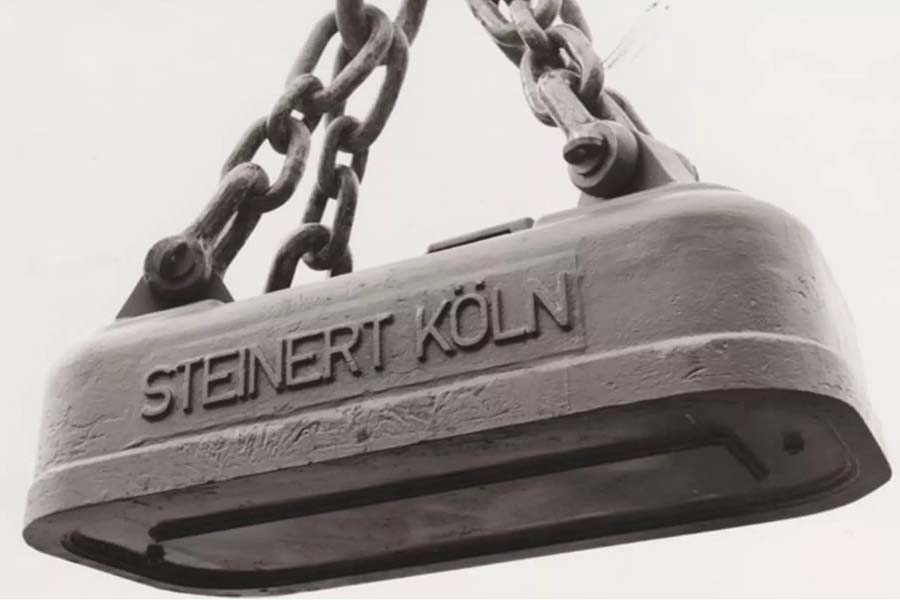