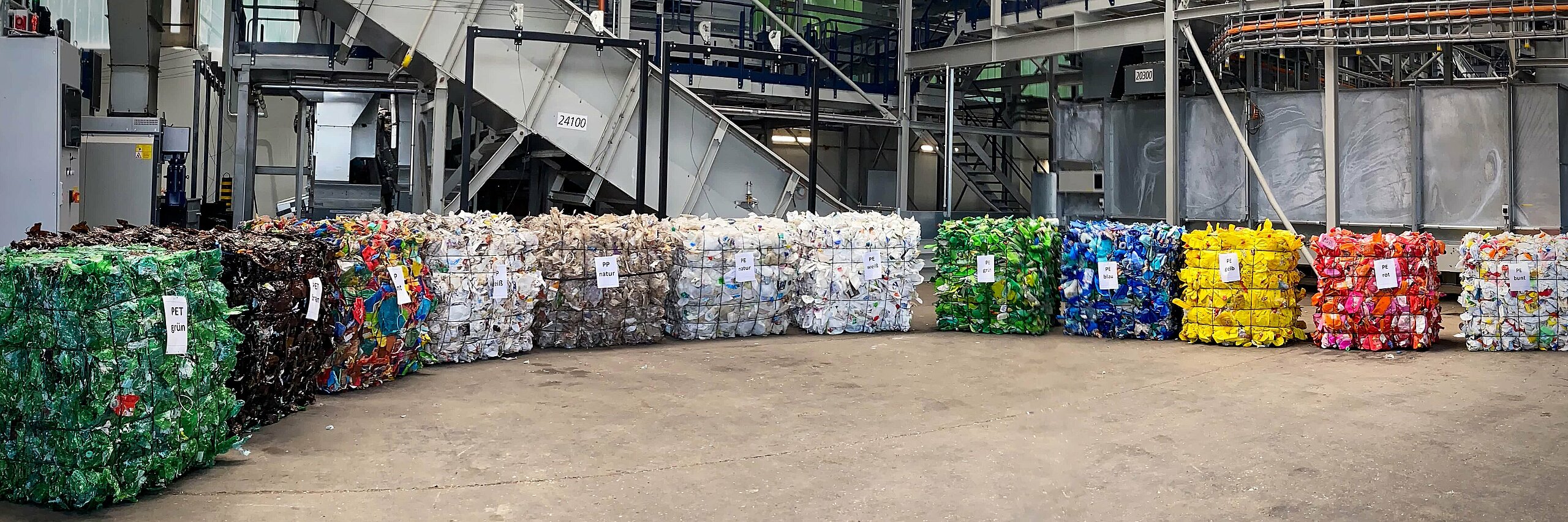
AI-based sorting technologies from STEINERT create new cycles at RE Plano
RE Plano, a subsidiary of the REMONDIS Group, is using STEINERT separation and sorting systems in its latest sorting plant in Bochum, Germany, to create closed cycles for polyolefins, as has already been achieved in the industry for PET. STEINERT's AI-based sorting technology paves the way for new closed-loop applications for plastic fractions that are particularly difficult to sort.
The aim for closed cycles
RE Plano has the ambitious aim of recreating the success of the circular economy achieved with polyethylene terephthalate (PET) for the materials polyethylene (PE, HDPE) and polypropylene (PP). To achieve this aim and to be able to operate the facility cost effectively, plastic fractions have to be sorted to purities of over 97% – according to type and colour of the plastic. Unfortunately these are often neglected due to the difficulty distinguishing between them (such as white and natural-coloured plastics as well as single and multi-layer packaging). Dr. Harald Lehmann, Business Development & Branch Manager at RE Plano Bochum, praises the collaboration:
With STEINERT’s support, we have found a solution that goes beyond the legal requirements and pushes the boundaries of what is possible in plastics sorting.
The cooperation is an important step towards a sustainable future in which resources are reused again and again.
Technology and efficiency
AI-based sorting technology and highly integrated processes enable a high level of efficiency. A majority of the plastics to be processed originate from REMONDIS’ sorting facilities for post-consumer packages and are further prepared within the company and processed into high-quality recyclates (PCR). The AI-based STEINERT technology Intelligent Object.Identifier combines colour sensor and near-infrared sensor (NIR) with hyperspectral imaging (HSI) technology. The unique combination not only enables a flexible response to future requirements, but also opens up new opportunities for additional sorting tasks that were previously not possible using conventional processes. This includes the sorting of difficult-to-distinguish plastic fractions and the separation of silicone cartridges, which could contaminate a PE plastic fraction to the point that it is unusable. The technology enables sorting on a new level thanks to additional characteristic properties that can be identified visually, supporting RE Plano’s vision of creating closed cycles for PE and PP with technological innovation and efficiency.
Results and sustainability
The result of the partnership is a state-of-the-art sorting facility which is among the most modern plastic recycling initiatives in Europe. “After a construction period of only six months, we have succeeded in creating a sorting facility that enables improved processes for moving towards more uniform, pure-grade plastics through highly efficient sorting”, stresses Dr. Harald Lehmann. The facility can sort around 30,000 tons of plastics per year and is therefore an important step towards a circular economy for plastics. It embodies the joint mission of STEINERT and RE Plano of pushing the limits of feasibility in plastic sorting and shaping a sustainable future in which resources can be reused in an infinite cycle.
About Steinert
The history of STEINERT dates back more than 130 years: the family-owned, Cologne-based business is one of the world's leading experts in sensor sorting and magnetic separation for waste and metal recycling as well as mining. With 450 employees, STEINERT generates an annual turnover of approximately EUR 180 million. In addition to 50 sales partnerships and joint ventures across the globe, the company has subsidiaries in Germany, Australia, Brazil and the USA.
Media contact
Marianne Grub
Marketing Manager