
UniSort PR EVO 5.0®
NIR sorting unit with hyperspectral imaging camera technology
State of the art – camera-based NIR technology for even better sorting results
It is now over 20 years ago that the first near infrared (NIR) detection systems, originally developed for the food industry, found their way into recycling. A lot has happened since then both in terms of the available sensors and the evaluation algorithms being used:
Mobile phones recognise their legitimate users via the built-in camera and vehicles drive autonomously on our motorways. These are just two examples of the rapid development in sensor-based applications.
It was only a matter of time before camera-based systems also became standard in NIR sorting units, given the large number of developers dealing with these issues worldwide.
Early in 2012 the first UniSort PR series replaced the point-to-point scanner, which had been usual until then. The UniSort PR from STEINERT uses an hyperspectral imaging (HSI) camera that has a previously unheard of visual and spatial resolution.
The fifth evolutionary stage of the tried-and-tested UniSort PR builds on this foundation, refines it and paves the way into the next era of waste sorting technology.
The UniSort PR EVO 5.0 reflects STEINERT’s years of experience gained from several UniSort generations and the huge amounts of data that have been processed. This forms the basis for further advances in sorting performance, but also for optimising processes in the value-added chain. This in turn enables users to respond flexibly to changing material flows and recognise but also most importantly tap into new potentials.
The five most important new features of the UniSort PR EVO 5.0 at a glance:
- Revamped light boxes
- Enhanced valve manifold
- Dynamic calibration
- Automatic white balance
- Object recognition
The model has been put through its paces in practical trials since the start of 2018, and is the next logical step in the evolution of sorting machines. It is also a showpiece of modern technology and robust engineering work. Alongside a whole host of detail improvements, the latest iteration features a design which is much easier to maintain and delivers advanced sorting results.
Dynamic calibration monitors the spectrum of the belt lighting, which is changing all the time in response to external factors, and does so without interrupting the sorting process. Revamped light boxes ensure improved detection in the long term while also simplifying maintenance. Coupled with software updates that are being developed all the time, optimised valve blocks then guarantee a consistently precise separation of the waste flow. An optional automatic white balance reduces the intensity of maintenance, eliminating further manual stages, thereby improving staff management and making new levels of flexibility possible.
Greater efficiency using proprietary STEINERT software
- Use of the full spectrum
- Individual adaptation to the material being sorted
- Precise detection using a combination of NIR and colour cameras
- Detection of materials that are particularly difficult to distinguish between, such as PET bottles and trays, along with silicone cartridges
- AI-supported object recognition
Because the software used for evaluation is an in-house development, the application range made possible by HSI technology can also be fully exploited and the sorting task can be rapidly adapted to your individual needs. Long development loops with external suppliers are therefore superfluous.
Even the smallest differences in the chemical composition of the detected materials can be assessed since the HSI technology we deploy is able to analyse these typical patterns at very fine resolutions.
In addition, the high spectral resolution makes the UniSort PR’s detection system much more resilient against moisture. Water has a very significant wavelength in the NIR range, so it can slightly overlap the actual signal of the target object at a lower spectral resolution.
Sorting PET fractions
This is how for instance our UniSort PR can detect a difference between the chemical composition of a PET bottle and a PET tray when sorting a PET fraction. The system could for example be used to select the PET tray or other PET multi-layer as active in the sorting process and only the pure PET bottle fraction would then be transferred to the subsequent processing line. The downstream processing line – say a colour sorter or even a density separator – would consequently be less burdened with impurities, which greatly simplifies the sorting task and results in higher extraction and better purity in the PET bottle target fraction.
Sorting silicone cartridges
Some sorting applications cannot be handled using conventional methods – for example sorting silicone cartridges. Since they comprise a polyethylene (PE) outer wall, they are valuable materials for recycling. Silicone residues inside the cartridge can, however, contaminate pure PE products, even rendering them unusable, and meaning that they have to be removed from the material flow.
The Intelligent Object Identifier has been developed for precisely this initial application; an AI-supported object detection system for sorting machines that detects and isolates these cartridges using optically detectable characteristics. These additional distinguishing features make for a more stable sorting process, while also improving sorting results.
Widely applicable
In addition to these more complex applications, the UniSort PR can of course also be used for all typical NIR applications in the field of sorting plastics or plastic mixtures, the sorting of substitute fuels or in the green waste / waste wood sector. The UniSort PR is generally available in working widths of 1,000 mm, 1,400 mm, 2,000 mm and 2,800 mm.
A combined system is also available, which also provides the system with colour information in the visible range (VIS range) in addition to pure detection using NIR. This means for example that PET bottles can be sorted by their colour, or even milk bottles and paper.
As with all our UniSort solutions, the UniSort PR can also be integrated into a control system where all currently collected data like material composition, belt occupancy and material distribution can be delivered.
Downloads
Videos
Application examples
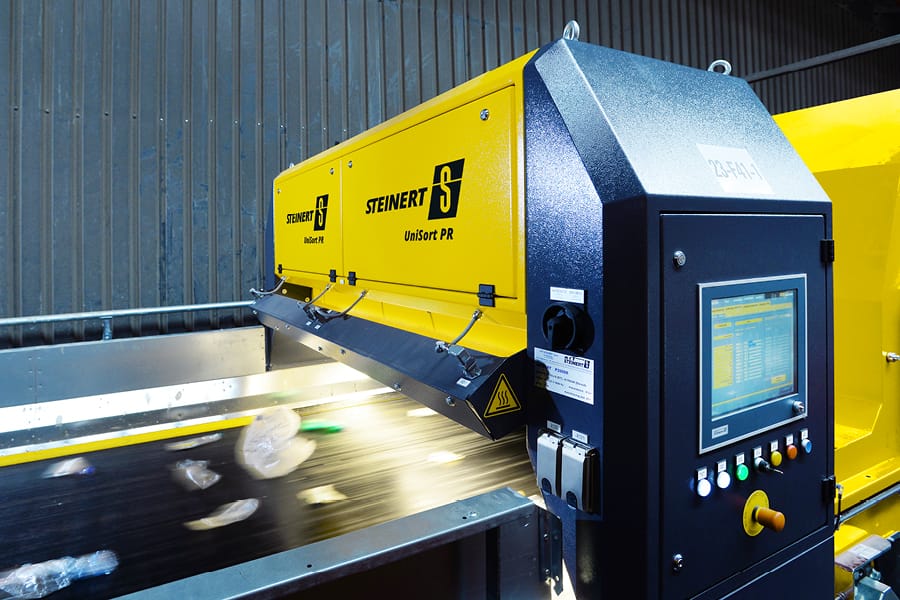
Waste recycling
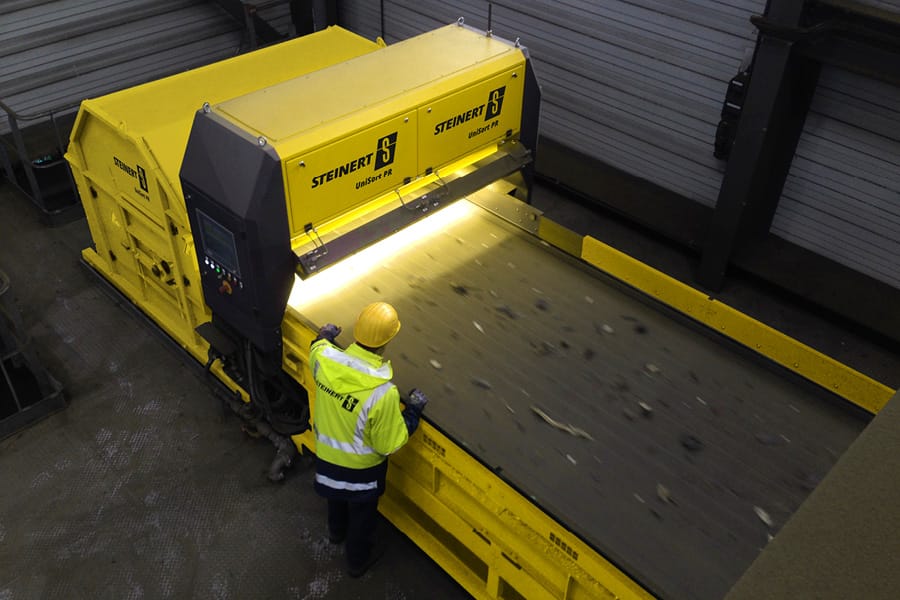