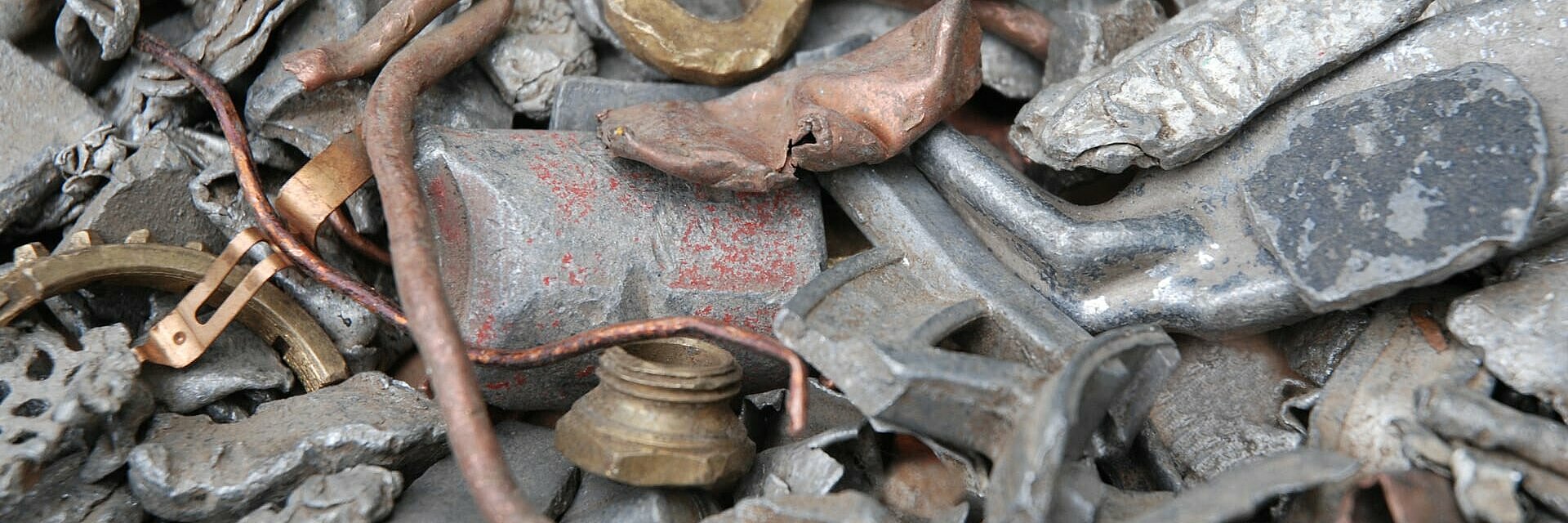
NON-FERROUS METALS
Sorting of non-ferrous metals
Recovery and quality improvement of non-ferrous metals for further processing and secondary smelting
An important role in the recycling of non-ferrous metals is played by the quality of the processed, segregated metals to ensure that they can be used in the smelter and to achieve added value and marketable products.
Recover non-ferrous metals with STEINERT EddyC
We offer you an efficient and effective solution for non-ferrous metal recovery with our STEINERT EddyC eddy current separator, which can be found in almost all metal recovery processes for metal recycling.
In its STEINERT EddyC FINES version, this non-ferrous metal separator is suited for fine grain sizes down to 0.5 mm. This is made possible by its precisely adjustable separating splitter mechanism, optimised to the drop parabola of the material stream. Combined with the trusted high-frequency pole drum with its eccentric construction, the highest yields and purity levels can be achieved. Regardless of whether it's non-ferrous metal recovery from waste incineration ash, e-waste, shredder operation or dry-mechanical sorting of mixed metal-bearing residues. The product (ZORBA) from this non-ferrous separator is a valuable input to further separate and upgrade the inherent non-ferrous metals. Customers for our non-ferrous products include dry-mechanical processors with X-ray transmission technology (XRT) such as STEINERT XSS T EVO 5.0, manual sorting plants, wet-mechanical plants or secondary smelting plants.
Wet-mechanical separation (also known as dense media separation (DMS) – the sorting of material by density using liquid separation media) of metals and contaminants achieves separation of non-metals and metals and also of light and heavy metals. The high heterogeneity of the input means that a simple wet-mechanical density separation is often not sufficient to efficiently separate circuit boards, cables or metal composites into one product fraction. These materials then end up in the DMS residues as well as in the aluminium product fraction, where they are lost as impurities. In an online or batch process, all material classes can be recovered with our STEINERT KSS combination sensor sorting system and sorted specifically into the individual fractions. Typical grain sizes here are +10 – 40 mm and +40 – 120 mm. A sensor combination, e.g. of a colour camera, metal sensor and 3D detection, records the properties of the individual objects and forms product classes tailored to the customer. These are stored as a sorting program.
The so-called heavy fraction of DMS is a very valuable mix of heavy metals such as copper, zinc, brass and stainless steel. Separation based on X-ray fluorescence technology is recommended, since surface contamination and coatings on this material make colour sorting only possible to a limited extent.
Sorting heavy metals using XRF technology (X-ray fluorescence)
The sorting of heavy metals into types through X-ray fluorescence (XRF) has proved itself in practice. Thanks to the easily detectable emissions spectrum of the metals under radiation with X-rays, the heavy metals can be separated by individual type: such as copper, brass, zinc (e.g. zamak - ZnAl 4%), lead, stainless steel and items containing gold and silver. Even mixed heavy metal concentrates from XRT and separation table processes are now best sorted into the individual metal types through XRF technology. Depending on the process engineering pre-treatment, material origin and composition, the STEINERT KSS | XF CL (belt machine) and the STEINERT CHUTEC | XF CL (chute machine) are design variants achieve the best possible sorting result. Coarser and heterogeneous material tends to be transported onto the belt grader, whereas the chute grader is primarily recommended for medium to smaller grain sizes and rolling material. This offers a wide range of sortable fractions in the grain size range down to 5 mm. The STEINERT LSS | XF line sorter is suitable for small to medium volumes of mixed heavy metals in a homogeneous grain size of 40-120 mm. The special feature of this machine is a special conveyor system in which all objects are detected one after the other and then pass through a series of side exits. This way, up to 7 sorting results or products can be achieved in one pass.
Top qualities of light metals due to X-ray transmission
Smelting operations involving secondary heavy and non-ferrous metals require pre-products that are as well-sorted as possible and defined alloys to enable adherence to the plant's technical demands and customer requirements. If the supplier's scrap is not sufficiently clean or too heterogeneous, in some cases it must be re-sorted . This might be aluminium scrap, zinc sheets or copper and circuit board scrap.
Aluminium and lightweight scrap metal that is delivered with elements of free heavy metals still present can be further purified using X-ray transmission (XRT) in our STEINERT XSS T EVO 5.0. Profiles, light aluminum scrap and twitch can be sorted economically in grain sizes between 8 – 150 mm. This enables accurate cleaning of aluminium scrap and reduces the proportions of zinc, copper, iron, free magnesium or brass.
Should light alloy elements be detected in the aluminium, appropriate sorting can be provided with our LIBS technology (laser induced breakdown spectroscopy). The STEINERT LSS | LIBS line sorting system can be used to separate aluminium alloys according to main alloy classes, for example on the basis of their magnesium or silicon content.
Your benefits:
- Recovery of non-ferrous metals using the STEINERT EddyCeddy current separator
- Sorting non-ferrous metals with sensor technology extends the recovery depth and added value
- Dry density sorting of non-ferrous metals into clean heavy and light fractions using X-ray transmission (XRT)
- Separate heavy metals by type using X-ray fluorescence (XRF)
- 3 different versions of X-ray fluorescence sorting systems are available (belt, chute and line sorters)
- Sort light metals by alloy classes using LIBS