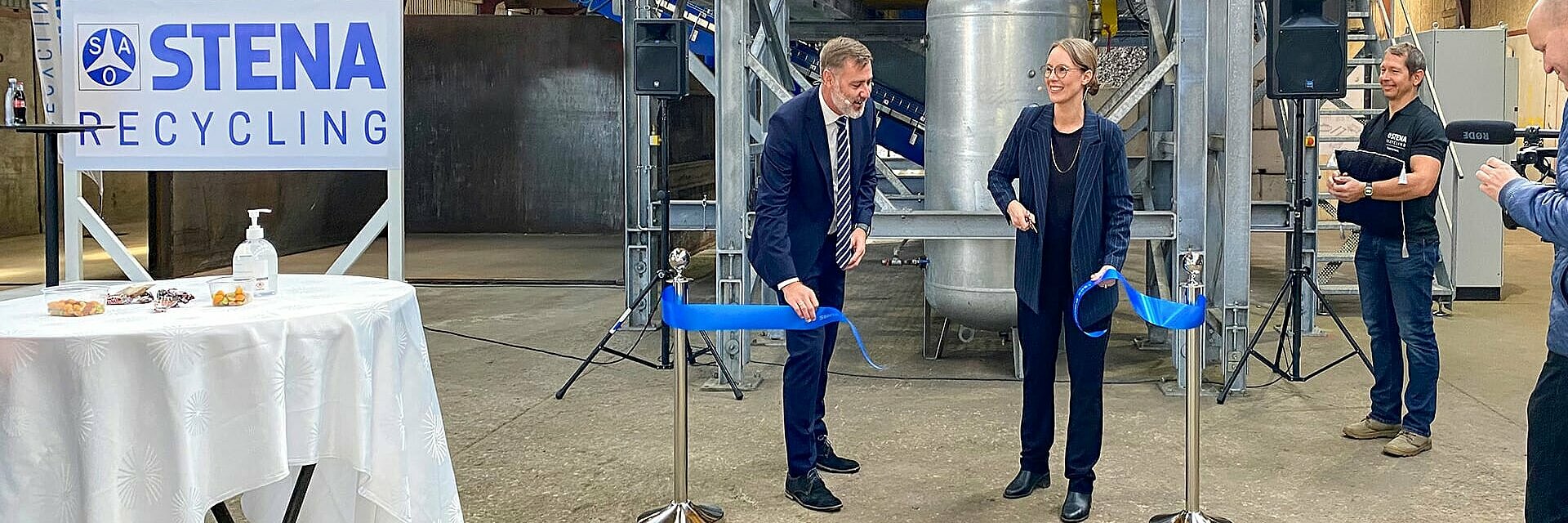
Technologie des rayons X et réduction des émissions de CO2 - quel est le rapport entre les deux ? Un entretien avec Stena Recycling.
La Ministre de l'Environnement danoise Lea Wermelin et Henrik Grand Petersen, CEO de Stena Recycling, ont officiellement inauguré le nouveau « X-ray Sorting Center » de Roskilde. Par la suite, la société Steinert s'est entretenue avec Jesper Fournaise, Outbound Sales Manager de Stena Recycling, pour expliquer pourquoi la séparation densimétrique à sec en utilisant la transmission de rayons X se conjugue avec la notion de durabilité.
Dans la ville de Roskilde, située à 30 km à l'ouest de Copenhague, le pionnier danois du recyclage des métaux fait confiance aux « rayons X » ou, plus précisément, à la technologie de transmission de rayons X développée par Steinert, pour la production d'aluminium ultra pur. L'aluminium, qui remplace de plus en plus de matériaux comme l'acier et qui est recyclable à 100 %, a de beaux jours devant lui. L'utilisation d'aluminium secondaire, également connu sous le nom d'aluminium vert, permet de réaliser des économies d'énergie pouvant atteindre 90 % lors de la production par rapport à l'aluminium primaire, soit l'équivalent de plusieurs tonnes de CO2 . Si de l'aluminium recyclé est utilisé pour la fabrication de nouveaux produits, les producteurs d'aluminium exigent toutefois un degré de pureté constant de la matière première secondaire. « C'est là un des défis que les technologies de tri savent résoudre », affirme Jesper Fournaise, responsable de la production et de la vente de l'aluminium. Le principal critère de différenciation qui intervient dans le tri utilisant la technologie des rayons X est la densité. La classification est très fine et permet de produire des métaux de haute qualité. Le système de tri utilisé à cet effet sert, par exemple, à la séparation de métaux lourds, de composants en aluminium, de magnésium libre et de l'aluminium forgé et coulé.
Qui dit développement technologique dit durabilité
« Nous sommes les dieux verts », déclare Jesper Fournaise lorsqu'il décrit son équipe. Il veut par là dire qu'ils transforment les ferrailles en matériaux recyclables qui réalimentent le circuit de production. Il devient très vite évident qu'il prend le sujet au sérieux. « Nul ne s'adonne au tri comme nous le faisons chez nous. C'est une pratique que nous enseignons aussi à nos enfants ». À la question de savoir quels ont été les principaux changements opérés ces dernières années, il répond : « Par le passé, les ferrailles étaient exportées vers l'Extrême-Orient où elles étaient triées à la main et on ne savait pas ce qu'il advenait des matériaux. Le développement des technologies de tri a changé la donne. En effet, grâce à la technologie des rayons X, nous pouvons désormais offrir des niveaux de qualité maximum et immédiatement réinjecter le métal dans le circuit économique de notre propre pays. »
Il n'est plus uniquement question du prix de vente d'un métal, explique Fournaise, mais aussi de gestion des flux de matière, comme par exemple la distance de transport. « L'utilisation de matières premières secondaires permet à nos clients, à savoir les fonderies, de réduire leurs émissions de CO2, et la phase de tri représente une des principales étapes préliminaires. » Pour finir, on compare le bilan écologique de la matière primaire à l'utilisation de matières premières secondaires. Pour Jesper Fournaise et son équipe, le critère absolu lors de leur production est la qualité, non pas telle qu'ils la définissent eux-mêmes, mais telle que la définissent leurs clients. « Ayant pour objectif d'atteindre des qualités semblables à l'aluminium primaire, nous avons opté pour la technologie de tri proposée par Steinert. Il ne fait aucun doute que la technologie de Steinert permet d'obtenir exactement les taux requis pour le cuivre, le zinc, le manganèse et le magnésium. Nous avons réalisé des essais et trouvé le niveau de qualité idéal pour nos produits. »
À la question de savoir quelle est la motivation de son équipe et selon quels critères ils prennent les décisions concernant les nouvelles technologies, Jesper Fournaise répond : « Les exigences de nos clients ». Et lorsque les idées deviennent plus concrètes, c'est le partenaire danois de Steinert, Viggo Bendz, qui est l'interlocuteur numéro un dans le processus d'innovation. Les essais réalisés dans le centre d'essais Steinert à Cologne aident au peaufinage des programmes de tri et pour la formation du personnel.
À propos de Steinert
L'histoire de STEINERT remonte à plus de 130 ans : l'entreprise familiale basée à Cologne est l'un des principaux experts mondiaux en matière de tri par capteurs et de séparation magnétique pour le recyclage des déchets et des métaux, ainsi que pour l'exploitation minière. Avec 450 employés, STEINERT réalise un chiffre d'affaires annuel d'environ 180 millions d'euros. Outre 50 partenariats commerciaux et coentreprises dans le monde entier, l'entreprise possède des filiales en Allemagne, en Australie, au Brésil et aux États-Unis.
Contact pour les médias
Marianne Grub
Responsable marketing