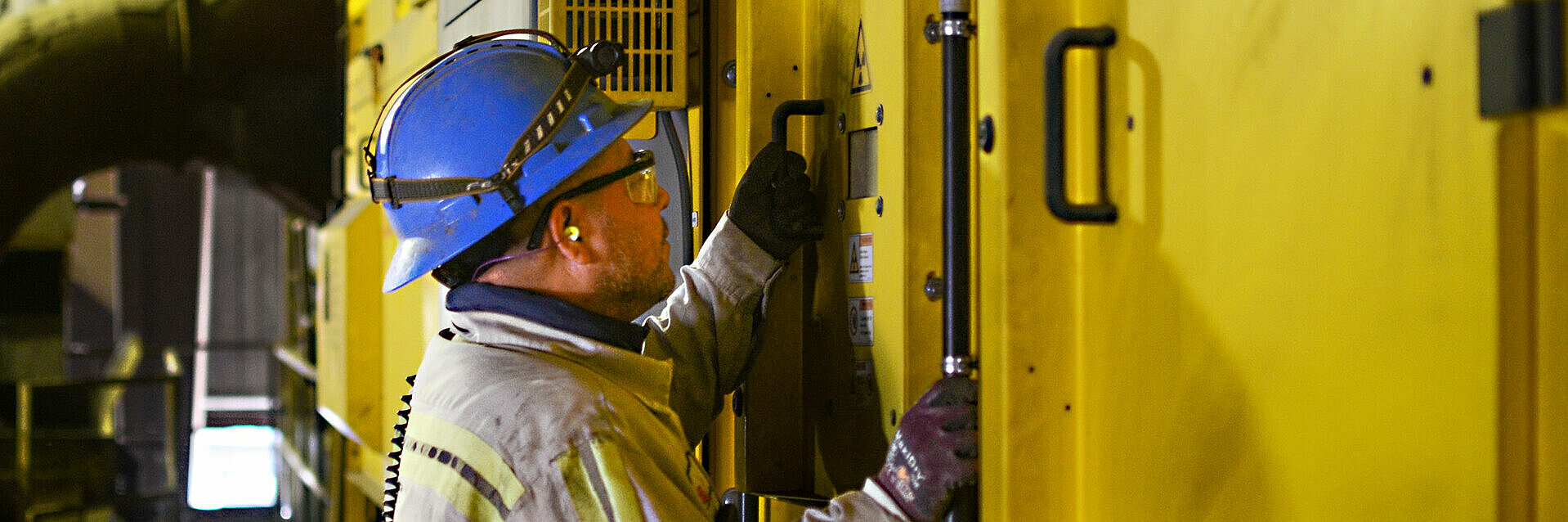
Précision et progrès : le parcours de la société SA Recycling avec la technologie de tri par capteurs STEINERT
SA Recycling est loin d’être une inconnue dans le secteur du recyclage. En effet, elle compte parmi les principaux acteurs nord-américains du recyclage des métaux, avec des activités qui s’étendent d’un bout à l’autre du pays. Chaque année, l’entreprise traite six millions de tonnes de ferrailles provenant des ménages et des commerces, et ce sur plus de 140 sites. Le PDG de SA Recycling, George Adams, a récemment accordé un entretien dans lequel il livre un éclairage sur la croissance de l’entreprise, ses efforts en matière de développement durable et le rôle déterminant des technologies de STEINERT dans ses activités. Omar Bravo, directeur général du centre de tri d’Anaheim en Californie, souligne les innovations fondamentales à la base du succès de l’entreprise.
Monsieur Adams, qui a fait ses premiers pas dans le recyclage à l’âge de 17 ans, a déclaré humblement :
J’ai débuté par la conduite de dépanneuses à 17 ans. Plus tard, j’ai commencé à travailler aux côtés de mon père et cela a duré une quarantaine d’années. Mes deux frères travaillent également dans l’entreprise et nous sommes partenaires. Nous sommes restés très proches, même après toutes ces années. Mes fils ont ensuite rejoint l’entreprise après leurs études supérieures. Je suppose que c’est ce qui fait l’intérêt de tout ça : à savoir travailler avec mes fils.
Toutefois, c’est George Adams qui, en fin de compte, a amené l’entreprise vers le succès remarquable qu’elle connaît. La participation de George Adams à des organisations internationales comme l’ISRI [Institute of Scrap Recycling Industries (institut des industries de recyclage des ferrailles, aux États-Unis)] et le BIR (Bureau International du Recyclage) met également en lumière l’engagement de l’entreprise sur le terrain politique afin de soutenir le développement durable à l'échelle mondiale.
Le parcours de la SA Recycling a débuté à Anaheim, Californie, où 250 000 tonnes de matériaux broyés sont traités chaque année. George Adams rappelle l’évolution et l’exension qu’ont connues les installations de l’entreprise, en soulignant le rôle d’Anaheim comme plaque tournante de la recherche et du développement pour SA. « En tant qu’entreprise de recyclage, nous sommes sans cesse en quête de meilleures solutions pour la récupération de matériaux, », explique Omar Bravo. « Le PDG George Adams a recherché puis acheté du matériel disposant des technologies les plus avancées pour atteindre cet objectif. »
Des systèmes de tri à haute fiabilité pour le traitement des métaux légers et lourds
Concernant les performances de tri, George Adams a loué la relation entre l’entreprise et STEINERT. « Cela fait quelque temps que nous utilisons leurs séparateurs à courants de Foucault sur nombre de nos sites pour récupérer la majeure partie de nos métaux non ferreux. Nous utilisons également leurs systèmes de tri multi-capteurs depuis environ quatre ans, principalement pour la transformation du Zorba en Twitch, c’est-à-dire pour extraire un mélange d’aluminium d’un flux de métaux non ferreux. » Le STEINERT KSS | XT CLI combine quatre capteurs. Deux capteurs optiques fournissent des données sur les couleurs et les formes tri-dimensionnelles, tandis que le capteur inductif détecte les métaux. Les différences de densité sont identifiées par la transmission de rayons X (XRT). Omar Bravo, quant à lui, souligne la flexibilité et la précision hors pair de cette technologie : « Nous sélectionnons le programme adapté au produit demandé par notre client, pour trier jusqu’à 99 % d’aluminium pur ou pour éliminer le magnésium du flux de produit sur simple pression d’un bouton. »
La technologie de fluorescence de rayons X (XRF) est également utilisée à Anaheim. Depuis 2019, la machine de tri STEINERT CHUTEC XRF sépare efficacement les métaux lourds en types de métaux tels que le cuivre, le laiton, le zinc ou l’acier inoxydable, ce qui ouvre de nouvelles perspectives de ventes pour SA Recycling. Et Omar Bravo de poursuivre : « Je pense que nous avons été la première entreprise de recyclage aux États-Unis à posséder ces machines et cela nous a ouvert les portes vers différents marchés. »
Tandis qu'Omar Bravo se félicite de la longévité des machines de tri à rayons X dont il n’a pas encore eu à remplacer un seul capteur en quatre ans, George Adams, de son côté, ne tarit pas d’éloges sur les séparateurs à courants de Foucault : « Lorsque nous avons commencé les mesures, ce qui nous a marqué était le fait que la vitesse de bande de leur machine était supérieure à celles de la concurrence. Plus impressionnant encore est de constater qu’au fil des années, nous n’avons perdu aucun roulement sur les séparateurs à courants de Foucault : ils sont tout simplement incassables. »
Ils sont tout simplement incassables.
Haute précision dans la séparation des métaux pour un avenir meilleur
George Adams considère que l’avenir n’est pas juste une destination, mais un parcours complexe. Il partage sa vision d'un écosystème global qui s’étend au-delà du recyclage du métal, évoquant non sans fierté l’engagement de SA Recycling à tout recycler, y compris l’eau qu’elle utilise dans ses enceintes et qu’elle réinjecte dans ses broyeurs pour la transformation de ressources de valeur. Bien qu’il admette que l’énergie solaire constitue une étape positive, Adams s’attache à maximiser le recyclage des métaux dans l’optique de réduire les gaz à effet de serre générés au cours de la production de métaux primaires, ce qui est bien plus profitable à l’environnement.
La collaboration avec des pionniers de la technologie comme de STEINERT conduit SA Recycling vers un avenir où précision, développement durable et efficacité fonctionnent en parfaite synergie. Le PDG envisage l’avenir du recyclage des métaux avec confiance. À ses yeux, les progrès de STEINERT dans la technologie LIBS pour le tri des alliages d’aluminium traceront la direction que prendra le secteur, en privilégiant la séparation de grande précision et ainsi satisfaire la demande d’alliages spéciaux qui retournent vers les États-Unis. « Je pense que le plus dur maintenant va être de s’adapter à la phase suivante, qui nécessitera du matériel conçu pour séparer les alliages spéciaux entre eux. À mon avis, c’est à ce niveau que se jouera véritablement l’avenir du recyclage des métaux. Tout le monde veut obtenir des alliages distincts. »
George Adams reconnaît le rôle que joue STEINERT dans l’amélioration des process de recyclage, tout en soulignant la ferme résolution des deux entreprises à répondre aux demandes croissantes du marché. Cette collaboration illustre l’importance de la technologie de pointe allemande pour faire avancer les efforts de recyclage à l’échelle mondiale. Sa confiance dans les capacités de STEINERT reflète sa conviction profonde dans l’ingénierie allemande. « Le Made in Germany n’est pas une notion creuse pour moi », explique Adams avec un hochement de tête. « STEINERT incarne ce label à la perfection. »
À propos de Steinert
L'histoire de STEINERT remonte à plus de 130 ans : l'entreprise familiale basée à Cologne est l'un des principaux experts mondiaux en matière de tri par capteurs et de séparation magnétique pour le recyclage des déchets et des métaux, ainsi que pour l'exploitation minière. Avec 450 employés, STEINERT réalise un chiffre d'affaires annuel d'environ 180 millions d'euros. Outre 50 partenariats commerciaux et coentreprises dans le monde entier, l'entreprise possède des filiales en Allemagne, en Australie, au Brésil et aux États-Unis.
Contact pour les médias
Marianne Grub
Responsable marketing